Mortar & Chamotte: it’s a match!
For mortar and fireclay to form a stable bond, the technical properties of both products must be optimally matched.
This is precisely what we offer.
Current offer
Our mortars are currently available at a particularly good price…
We are extending our mortar promotion! Until the end of the year, you will receive a 10% discount on your mortar order and pay no small quantity surcharge.
Our sales team will be happy to take your order by e-mail:
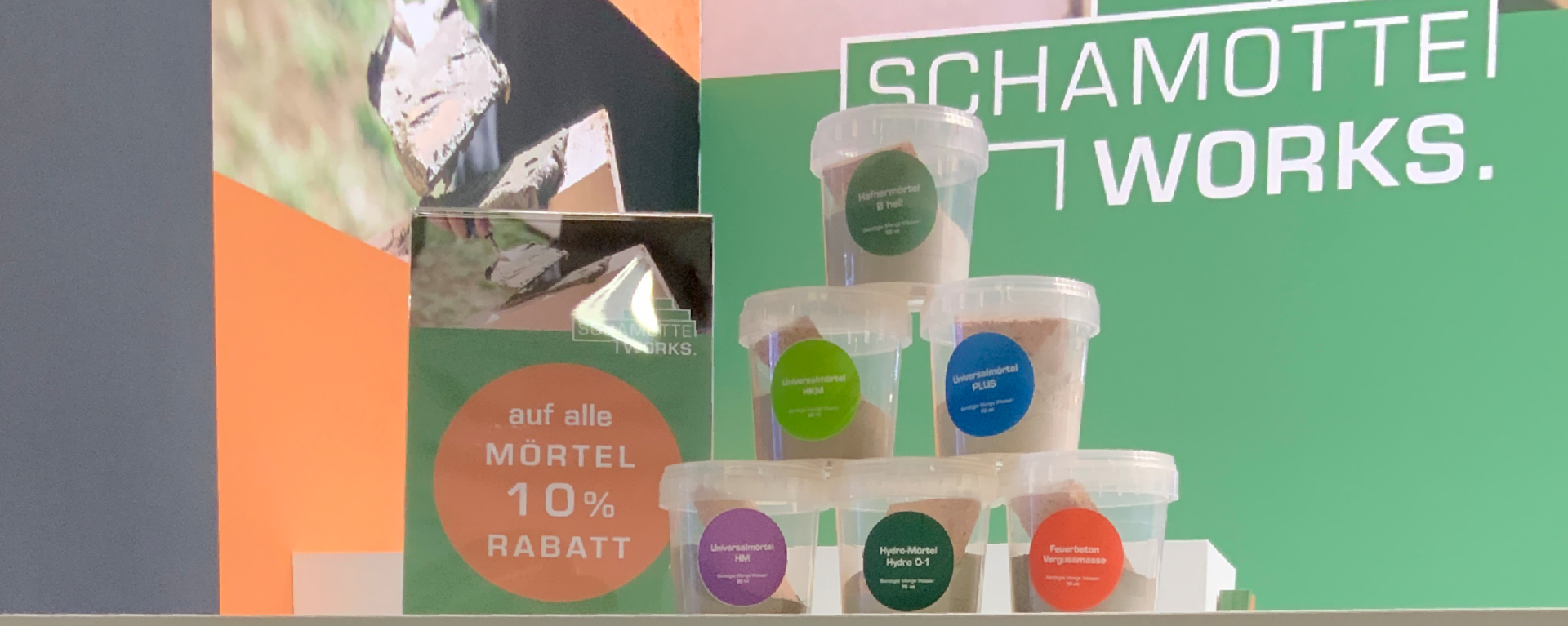
Our current mortar campaign:
Until the end of the year, you will receive a 10% discount on your mortar order and pay no small quantity surcharge.
See for yourself the quality and order our mortar at a special price.
Our sales team will be happy to take your order by e-mail:
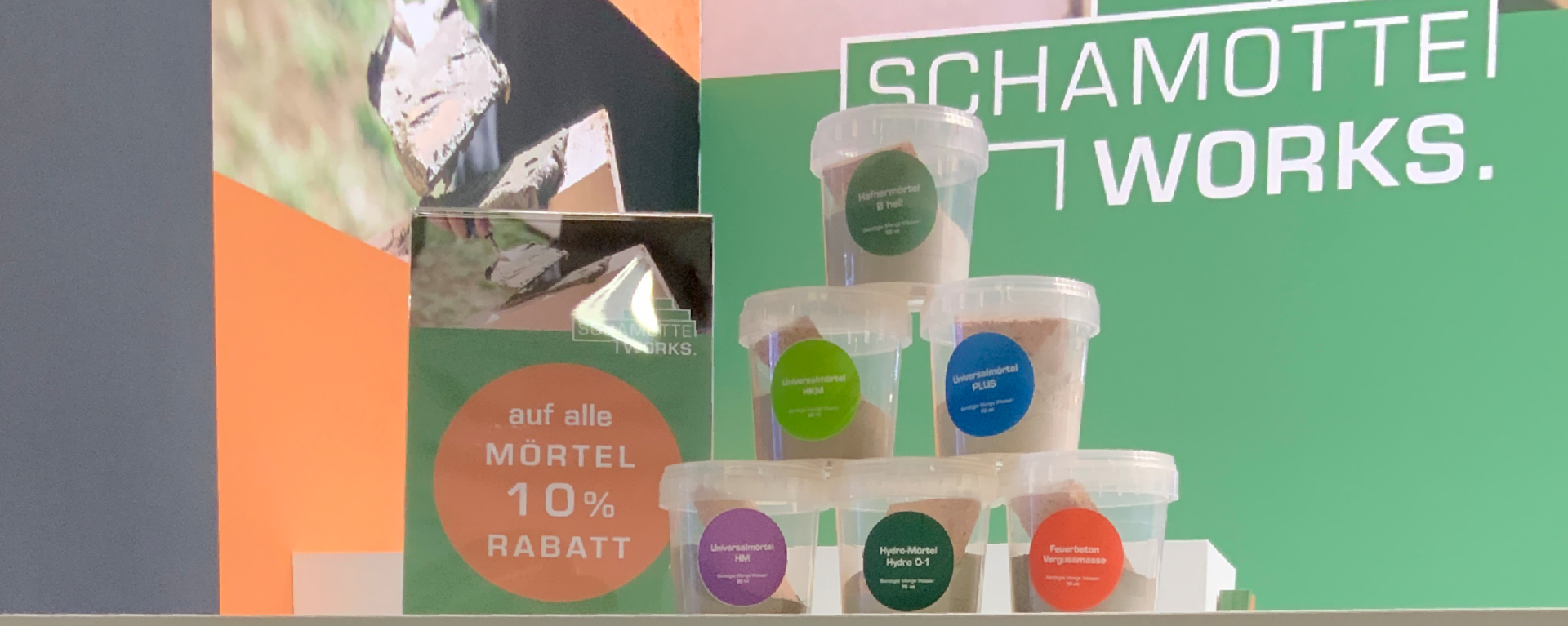
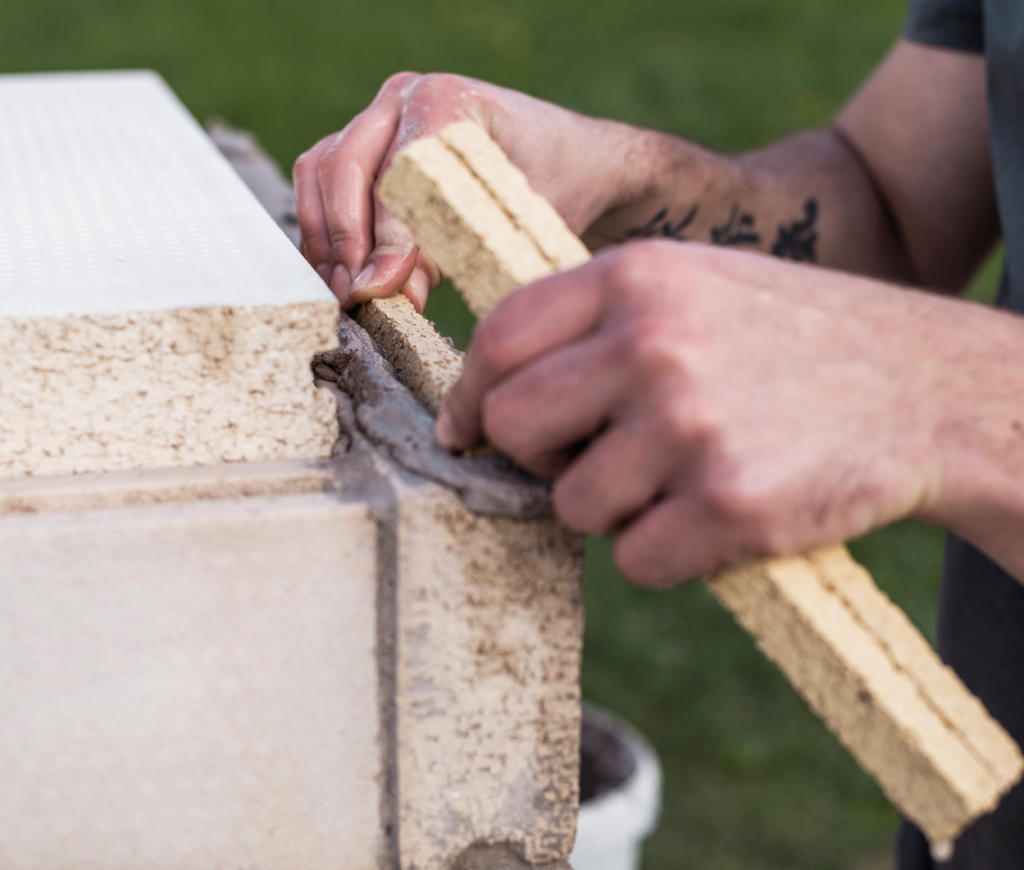
For all requirements from the furnace to the outer shell
Here you will find both universal mortars, which meet all requirements from the furnace to the outer shell, as well as other mortars and masses for special applications, e.g. hydro-mortar, refractory concrete, fibre mortar, fire-resistant glue or sealing compound. We also offer stove plasters for designing the outer shells.
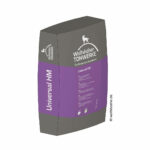
Universal mortar HM
for bonding robust outer shells, lining heating inserts and for installing supplementary ceramic heating flues
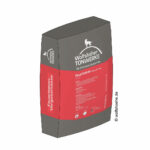
Refractory concrete sealing compound / ramming mixture
for repairing furnace floors, stove construction materials, arranging tiles and modelling
FAQs
Frequently asked questions about our fireclay
Fireclay is a purely natural material consisting of just three ingredients: clay, fired clay and water – nothing else. And yet not all fireclay is the same. Depending on the application, it has to meet very different requirements: sometimes it has to be particularly strong, sometimes particularly easy to work with, sometimes very fire-resistant and sometimes resistant to temperature changes, sometimes rather porous and sometimes rather dense. We guarantee this by mixing and processing selected clays very precisely according to sophisticated recipes, depending on the individual product.
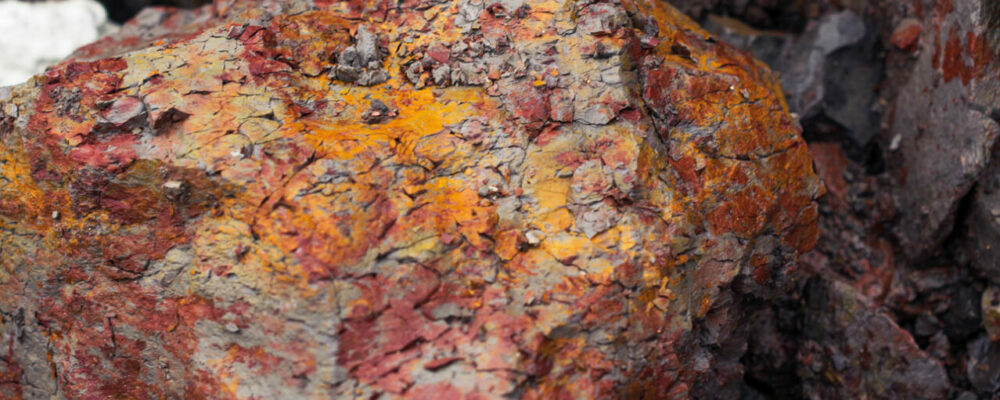
Our fireclay is used where high temperature stability and temperature change resistance as well as a high heat storage capacity are required. For example, for wood-burning stoves (heat saving stoves, basic stoves, hot-air stoves, etc.) in the combustion chamber, the flues or the outer shell; but also for the construction of wood-burning baking stoves or pizza domes. Chamotte is also used to protect the metal walls in the combustion chambers of wood-burning stoves, boilers, heating inserts and chimney inserts for solid fuels. These are usually individually tailored bricks, so-called shaped chamotte bricks. The inner pipes of chimneys are also often made of fireclay.
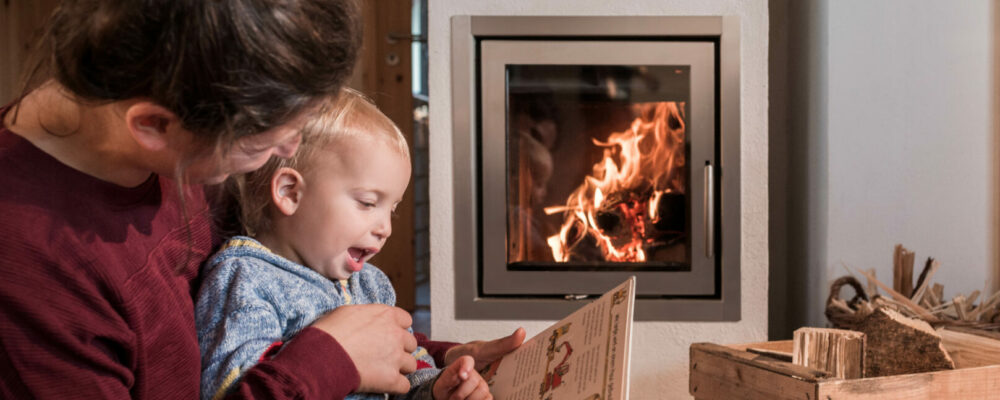
Our high-quality fireclay is characterized by its easy-to-use features. A whole range of tools is suitable for cutting: from the chop saw, floor cutter, plunge saw, angle grinder, foxtail saw, hammer, grindstone and diamond stone up to the wet cutting machine. Are you interested in more details? We show all options with their respective advantages and disadvantages in this video: https://www.youtube.com/watch?v=3FOBacPhZtk&t=659s
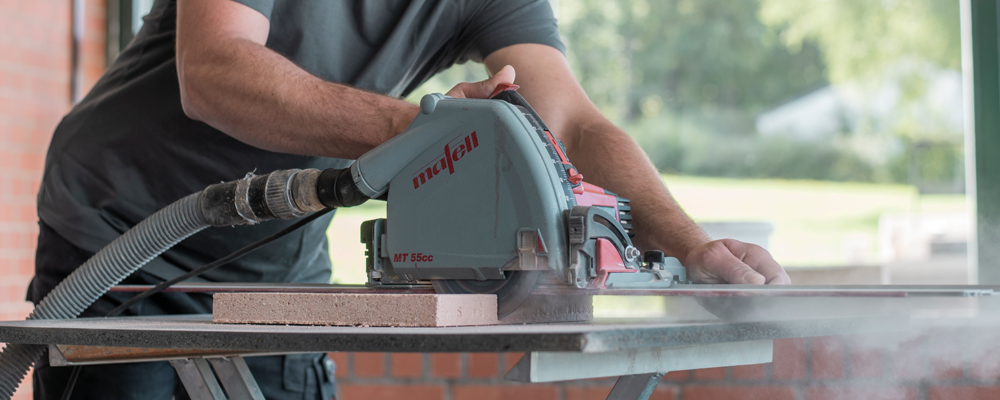
If you would like to use fireclay in such a way that it comes into contact with food, for example in a baking stove, then we recommend our WKS, HBO+ and HBW qualities. They meet the requirements for materials intended to come into contact with food. These qualities are therefore ideally suited for the construction of baking stoves for stone-baked pizza or stone-baked bread.
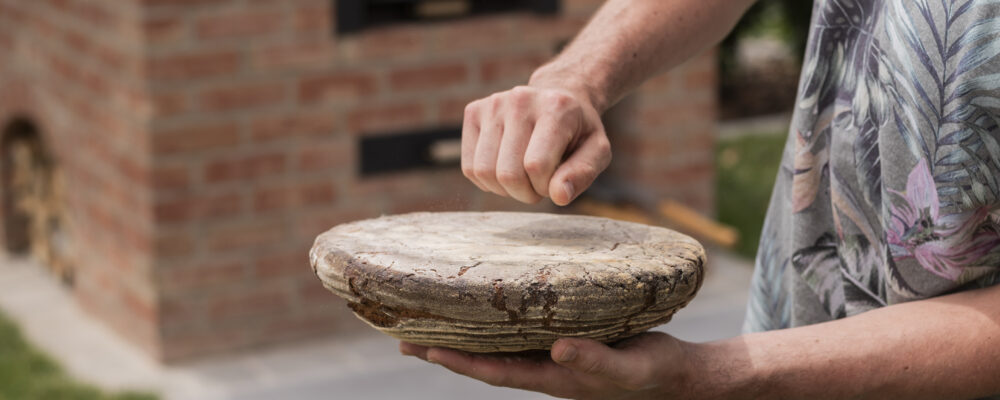
HBO+ is our light red standard quality and gets its characteristic colour from our domestic raw material, which we extract ourselves locally. It is suitable for all applications in the field of tile stove construction – from furnace to fl ue construction and the outer shell. Application temperature: 1,200 °C, density: 1.9 kg/dm3
WKS is a light yellow fireclay whose technical properties are comparable to our standard fireclay. It additionally corresponds to Austrian standard B 8306. It is suitable for all applications in the field of tile stove construction – from furnace to fl ue construction and the outer shell. Application temperature: 1,200 °C, density: 1.9 kg/dm3
HSM massiv is a red-brown heavy fireclay. Its technical properties make it an exceptional heat storage material. In tiled stove construction, it is particularly suitable for the flues and the outer shell. Application temperature: 1,000 °C, density: 2.4 kg/dm3
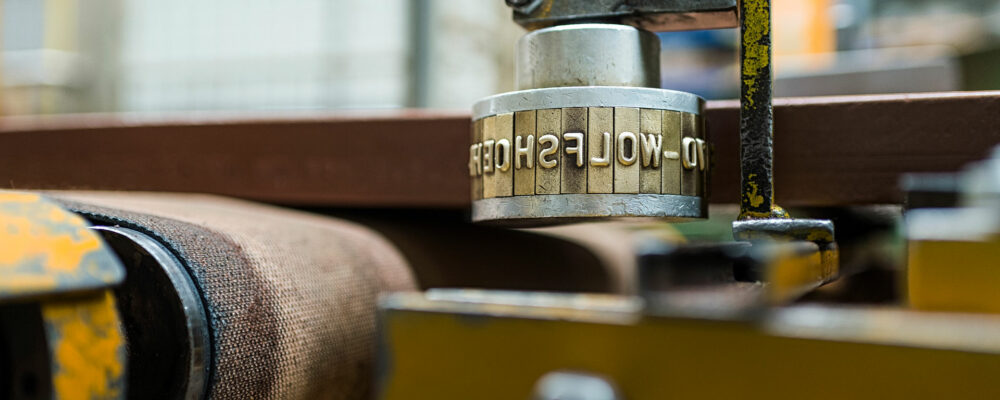
Our manufacturing processes result in different surfaces on our fireclay bricks and plates. Extruded fireclay has wire-cut (rough) and smooth surfaces. Repressed bricks are smooth on all sides. Selected bricks and plates are available with a dovetail profile.
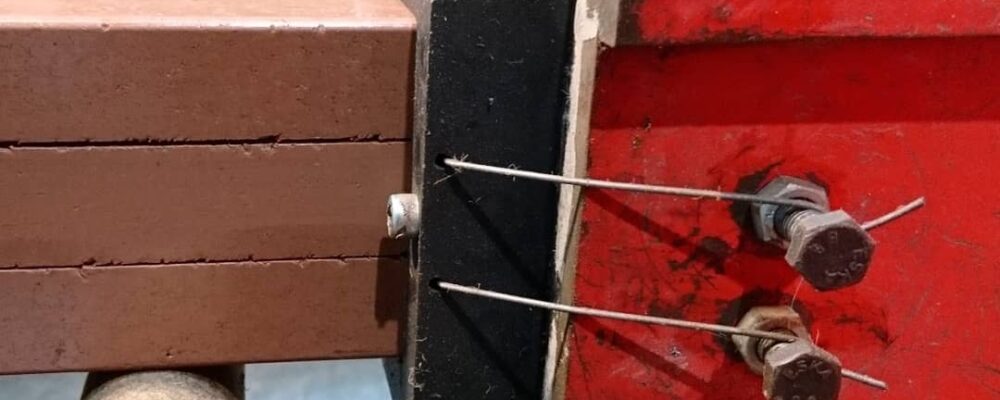
The fireclay from Wolfshöher Tonwerke is 100% “made in Germany”. With over 160 years of company history, we are one of the oldest manufacturers of refractory products in Germany. We have always produced the fireclay on the “Wolfshöhe” in Neunkirchen am Sand near Nuremberg. To this day, all departments of the company are located at the founding location in Franconia. The raw materials are also obtained locally, parts of them from the own clay pit. The entire manufacturing process is subject to strict controls by experts from our in-house laboratory – from the monitoring of the raw materials to the mixed compound up to the fired product. All parameters that affect the ceramic properties are inspected several times a day. Thereby, we constantly guarantee the highest quality.
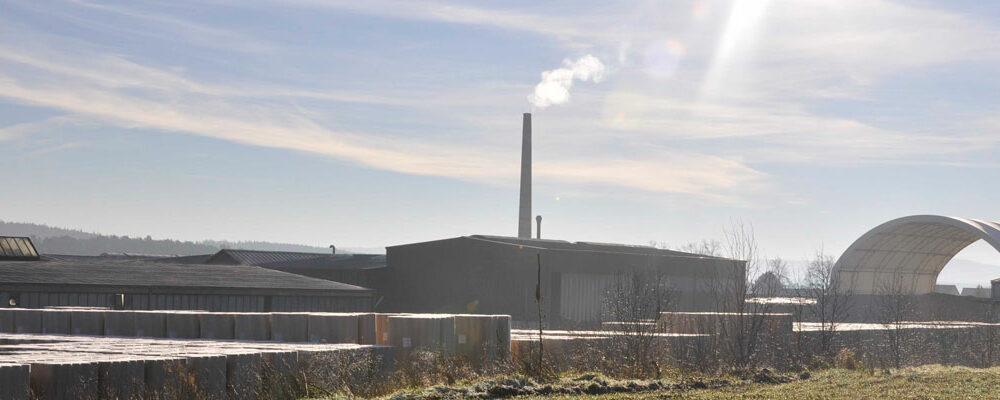
Our fireclay is used where high temperature stability and temperature change resistance as well as a high heat storage capacity are required. For example, for wood-burning stoves (heat saving stoves, basic stoves, hot-air stoves, etc.) in the combustion chamber, the flues or the outer shell; but also for the construction of wood-burning baking stoves or pizza domes. Chamotte is also used to protect the metal walls in the combustion chambers of wood-burning stoves, boilers, heating inserts and chimney inserts for solid fuels. These are usually individually tailored bricks, so-called shaped chamotte bricks. The inner pipes of chimneys are also often made of fireclay.
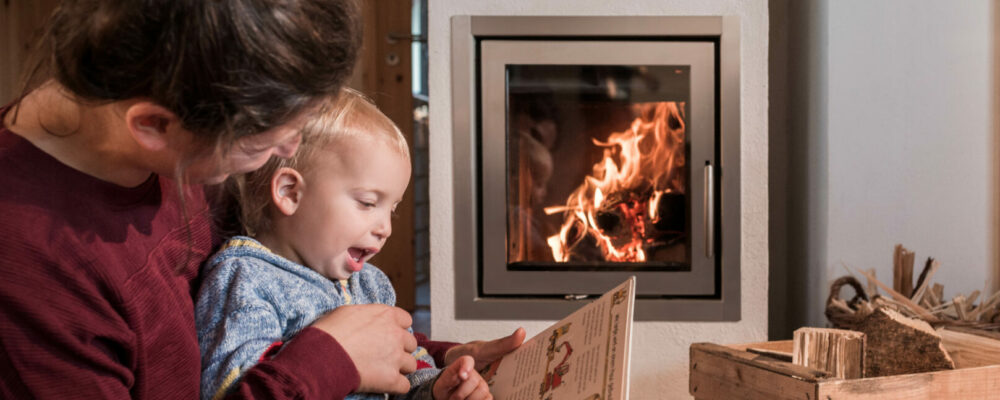
Our high-quality fireclay is characterized by its easy-to-use features. A whole range of tools is suitable for cutting: from the chop saw, floor cutter, plunge saw, angle grinder, foxtail saw, hammer, grindstone and diamond stone up to the wet cutting machine. Are you interested in more details? We show all options with their respective advantages and disadvantages in this video: https://www.youtube.com/watch?v=3FOBacPhZtk&t=659s
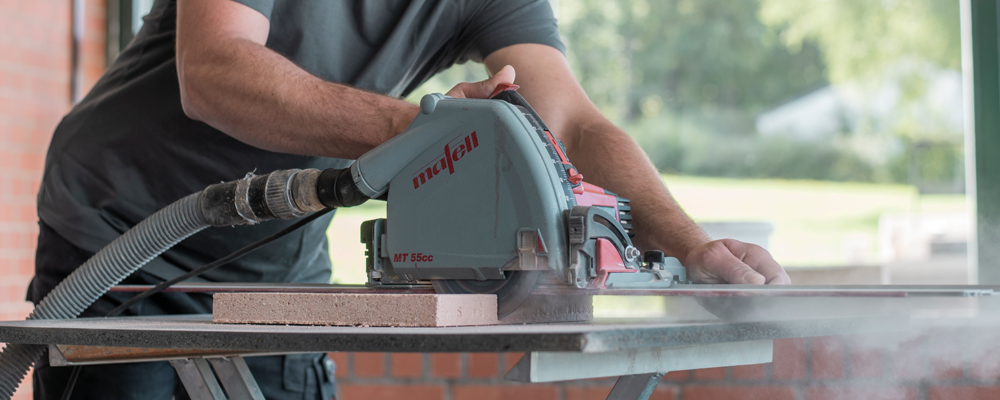
If you would like to use fireclay in such a way that it comes into contact with food, for example in a baking stove, then we recommend our WKS, HBO+ and HBW qualities. They meet the requirements for materials intended to come into contact with food. These qualities are therefore ideally suited for the construction of baking stoves for stone-baked pizza or stone-baked bread.
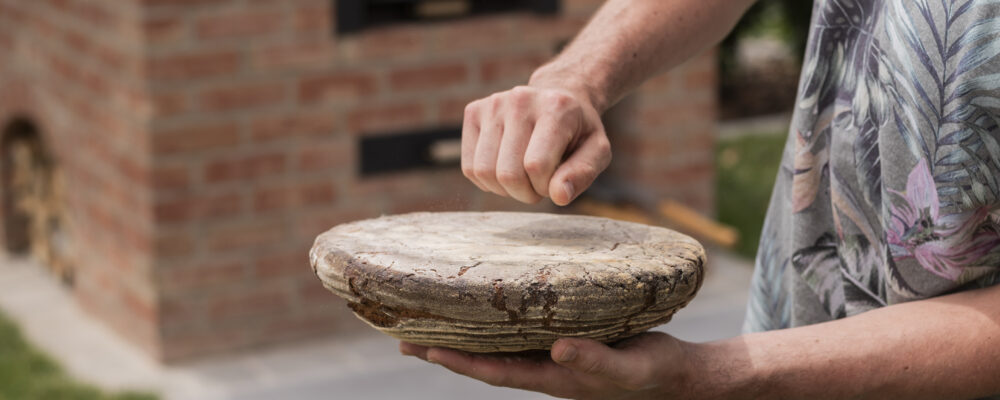
HBO+ is our light red standard quality and gets its characteristic colour from our domestic raw material, which we extract ourselves locally. It is suitable for all applications in the field of tile stove construction – from furnace to fl ue construction and the outer shell. Application temperature: 1,200 °C, density: 1.9 kg/dm3
WKS is a light yellow fireclay whose technical properties are comparable to our standard fireclay. It additionally corresponds to Austrian standard B 8306. It is suitable for all applications in the field of tile stove construction – from furnace to fl ue construction and the outer shell. Application temperature: 1,200 °C, density: 1.9 kg/dm3
HSM massiv is a red-brown heavy fireclay. Its technical properties make it an exceptional heat storage material. In tiled stove construction, it is particularly suitable for the flues and the outer shell. Application temperature: 1,000 °C, density: 2.4 kg/dm3
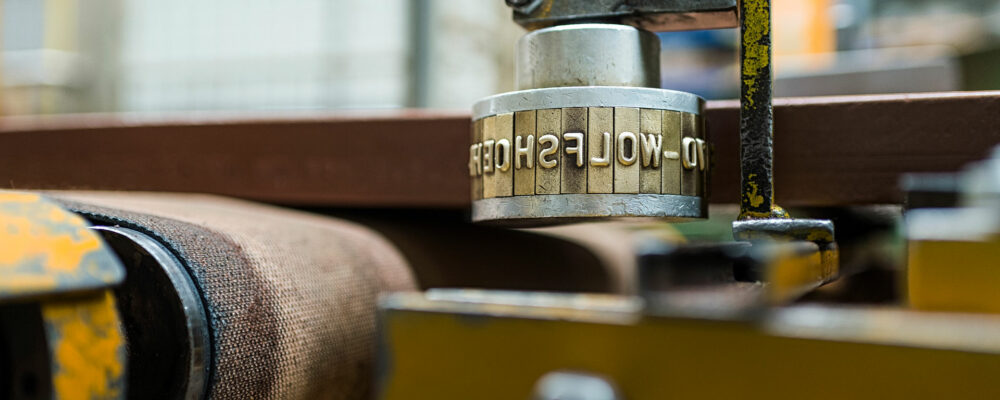
The fireclay from Wolfshöher Tonwerke is 100% “made in Germany”. With over 160 years of company history, we are one of the oldest manufacturers of refractory products in Germany. We have always produced the fireclay on the “Wolfshöhe” in Neunkirchen am Sand near Nuremberg. To this day, all departments of the company are located at the founding location in Franconia. The raw materials are also obtained locally, parts of them from the own clay pit. The entire manufacturing process is subject to strict controls by experts from our in-house laboratory – from the monitoring of the raw materials to the mixed compound up to the fired product. All parameters that affect the ceramic properties are inspected several times a day. Thereby, we constantly guarantee the highest quality.
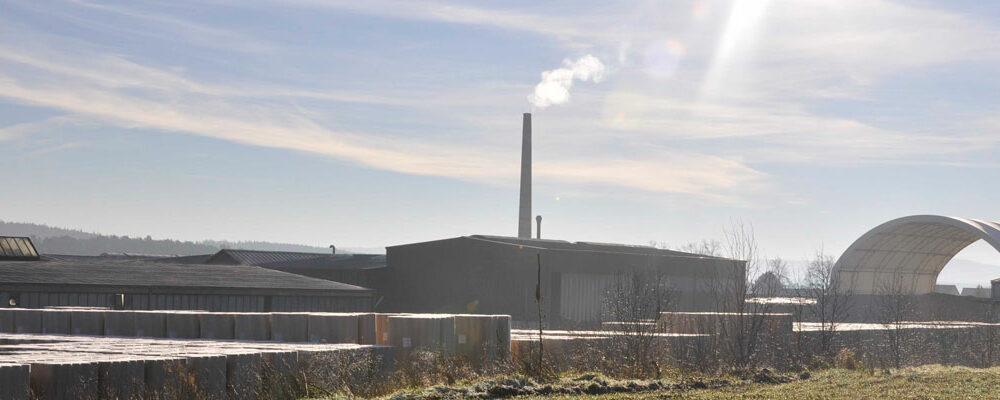
Fireclay is a purely natural material consisting of just three ingredients: clay, fired clay and water – nothing else. And yet not all fireclay is the same. Depending on the application, it has to meet very different requirements: sometimes it has to be particularly strong, sometimes particularly easy to work with, sometimes very fire-resistant and sometimes resistant to temperature changes, sometimes rather porous and sometimes rather dense. We guarantee this by mixing and processing selected clays very precisely according to sophisticated recipes, depending on the individual product.
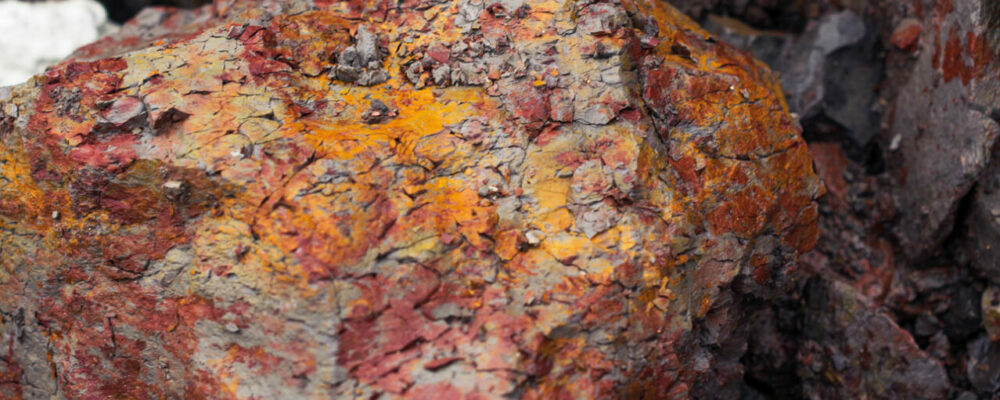
Our manufacturing processes result in different surfaces on our fireclay bricks and plates. Extruded fireclay has wire-cut (rough) and smooth surfaces. Repressed bricks are smooth on all sides. Selected bricks and plates are available with a dovetail profile.
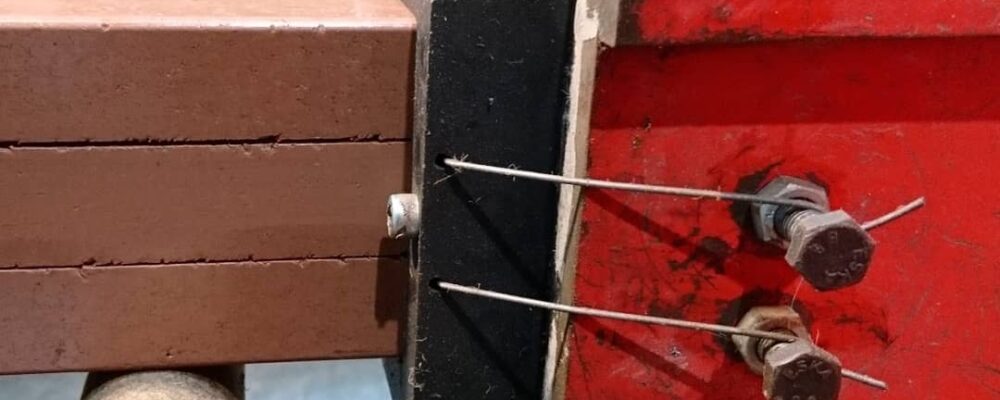